Monitoring the quality of fertilizer stock solutions
Hydroponic concentrated nutrient fertilizer manufacturers are not held to any routine quality standards by regulatory authorities in most countries. Although fertilizers need to be properly registered and their intended minimum compositions are shared with the public, the manufacturer never guarantees that each batch of the product will comply with any sort of quality standard and it’s therefore possible for hydroponic nutrients to come out of a factory with compositions that significantly deviate between batches. People who make their own fertilizers are also not free from problems either, as issues further down the chain – with the fertilizer raw inputs – or issues related with human error, can and will still happen.
Because of these problems, a very important part of every hydroponic grower’s process should be to establish some quality guidelines to evaluate whether a given batch of nutrients – either bought or self-made – complies with what is expected and can therefore be used in the hydroponic crop. In today’s post I will talk about the properties that you can measure in order to ensure that the quality of your inputs is sustained through time and how these measurements should be done.
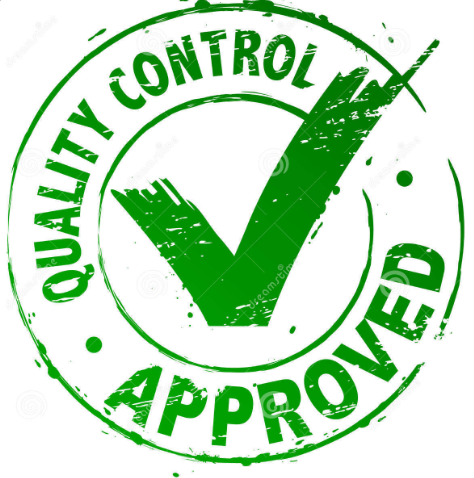
These are two measurements that should always be done whenever you receive or prepare a new batch of hydroponic nutrient stock solution:
Density of the stock solution: The density of a hydroponic stock solution should always be measured and recorded. The density needs to be measured accurately, using a pycnometer and an accurate enough balance (+/- 0.01g). A 5 or 10mL pycnometer would be recommended and the balance should be able to measure up to at least 50g, to ensure that the measurement of the final weight of the pycnometer will be in range. You should first weight the empty and dry pycnometer, then fill it with liquid to the brim, place the stopper – some liquid will spill, this is how it’s intended to work – then wipe any spilled liquid and weight the full pycnometer. The difference in weight divided by the pycnometer volume will give you the density. Make sure you also record the ambient temperature when the measurement is made.
pH of the stock solution: You can use a pH meter to determine the pH of a sample of the stock solution. You can use the regular pH tester you use to measure the pH of your hydroponic nutrient solutions, however make sure the pH meter does not remain for too long in the stock solution – more than what’s necessary to make the measurement – and wash it with distilled water and store it in pH meter storage solution as soon as the measurement is done. Also make sure the pH meter is calibrated right before making this measurement.
If any compounds are added incorrectly or the composition of the raw inputs was in anyway wrong, the above two parameters – pH and density – will tend to change, as they depend very strongly on the composition of inputs being the same. Of course, there are mistakes that can go undetected in these two domains but a stock solution that always records the same across batches will tend to be the same chemically. Every time you receive or prepare new solution record the above and ensure you never use any solution that deviates more than -/+ 5% from the median you have on your record. The deviation of the above two parameters also serves as a way to control how reproducible the manufacturing process of the stock solution actually is.
If there is a strong mismatch in these measurements when compared with the median of all past values, then you need to continue to actual chemical analysis of the nutrients to figure out what’s wrong.
If you prepared the fertilizer yourself then it becomes important to check notes – always keep records of weights that are added when preparing solutions – and see if there were any changes in the chemical suppliers of any of the used inputs. Sometimes the quality and composition of certain chemicals can change dramatically between suppliers, so making changes from one to another can often require chemical analysis to ensure that the composition stays the same. A good example can be potassium silicate, where the exact grade and potassium to silicon ratio of the raw material can change a lot depending on the exact fabrication process used by the company making it.
Another important point is the accuracy of the instruments used for the preparation of solutions. Sometimes the problem is that a scale or a volume measuring device lost calibration and generated errors in a previously unseen range. This can be particularly problematic if different instruments are used to measure different inputs, which can make some inputs subject to bigger errors that others and can therefore change the ratio between different nutrients in the hydroponic solution.