Never fail with ebb and flow hydroponic systems
Ebb and flow or “flood and drain” systems, are some of the most popular systems built in hydroponics. These are low cost, can host a large number of plants, and can generate good results, reason why they are a preferred choice for both new and experienced hydroponic growers. However, there are a substantial number of issues that can come up in these systems, both due to the different ways they can be built and because of failures in their management. In this post, I am going to give you some tips on the construction and management of ebb and flow systems so that you can minimize the chances of failure when building your own hydroponic setup of this kind. For some basics of how an ebb and flow system is set up, I advise you to watch this video.
Ensure full drainage
A common mistake when building a flood and drain system is to have incomplete drainage of the nutrient solution. Make sure you have a setup that allows for complete drainage of the solution as soon as a certain level is reached, and always stop pumps as soon as the return of the solution starts. It is quite important to also ensure that as little solution as possible remains at the bottom of your flood and drain trays or buckets, as plants sitting in puddles of water can be a recipe for disease and a very good environment for pests to develop. A very simple system I built in 2010 had the problem of never being able to efficiently drain, which caused substantial issues with the plants as root oxygenation was never as good as it should have been.
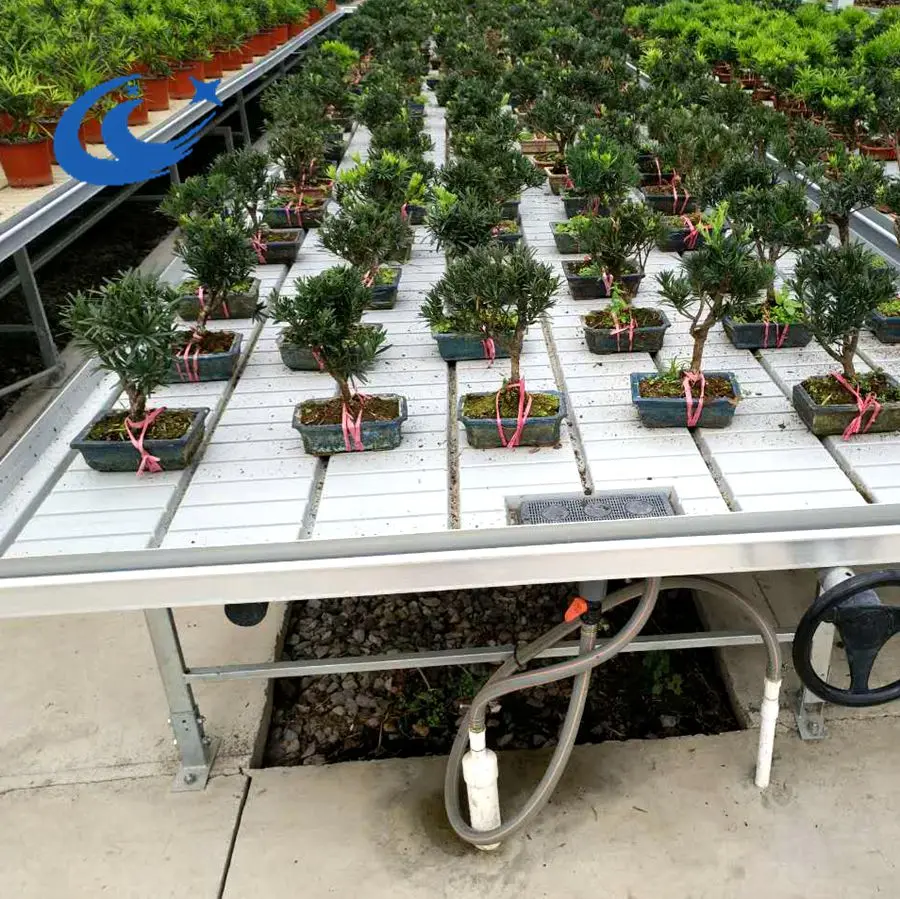
Fast cycle speed
Ideally, you would want the flood and drain cycle of an ebb and flow system to be as fast as possible. Also, the cycles should not take more than 15 minutes, from starting to flood the growing table to completely draining the system. For this, you need to have an adequately sized pump for the volume of your table that needs to be filled (total volume minus volume taken up by plants and media). If you want to use a smaller pump, you can always add some rocks to the table in order to take up volume and ensure you require to add less volume to fully flood the reservoir. Time your cycles and make sure these are as short as possible, adequately saturate the media and completely drain, as mentioned above.
The right media
A common reason why flood and drain systems are less productive is because of a suboptimal choice of media. Ebb and flow systems periodically flood the media with nutrient solution, completely saturating it with water, so media that retains too much moisture will require infrequent cycles and will be harder to time. Media like peat moss and coco are often inadequate for ebb and flow systems due to this fact, as over-saturation of the media will lead to periods of low oxygen availability for the plants. Media that drain fast generally do much better, choices such as rockwool or perlite can give much better results when compared with media that have much higher moisture retention. Since this is a recirculating setup, perlite and rockwool also have the advantage of being more chemically inert. I however do not like media that drain too fast, such as clay pellets, as these can require too frequent cycling.

Time irrigations with water content sensors
Your flood and drain system requires good timing of irrigation cycles in order to have optimal results. If you irrigate based on a timer, you will over irrigate your plants when they are small and will under irrigate them when they are big. Overwatering can be a big problem in these systems and it can be completely solved by both choosing the right media – as mentioned above – and using capacitive water content sensors for the timing of your irrigations. If you’re interested in doing this, check out this post I wrote about how to create and calibrate your own simple setup for using a capacitive water content sensor using an Arduino. This will allow you to flood your table only when it is needed and not risk over watering just because of a timed event happening.
Oversize the reservoir
The nutrient reservoir contains all the nutrition that is used by the plants, this means the bigger this is relative to the number of plants you have, the lower the impact of the plants per irrigation event will be. Having a reservoir that has around 5-10 gallons per plant – if you’re growing large flowering plants – or 1-3 gallon per plant, for leafy greens, will give you enough of a concentration buffer so that problems that develop do so slowly and are easier to fix. A large reservoir can fight the effects of plants more effectively and make everything easier to control.
Add inline UV sterilization
Disease propagation is one of the biggest problems of this type of system. Since recirculation continuously redistributes any fungal or bacterial spores among all the plants, it is important to ensure you have a defense against this problem. A UV filter can help you maintain your reservoir clean. You can run the solution through the inline UV filter on every irrigation event, ensuring that all the solution that reaches the plants will be as clean as possible. Make sure you use a UV filter that is rated for the gallons per hour (GPH) requirements of your particular flood and drain system. Also read my post about getting read of algae, to learn more about what you can do to reduce the presence of algae in a system like this.

Run at constant nutrient EC, not reservoir volume
One of the easiest ways to manage a recirculating system, especially with an oversized reservoir, is to keep it at constant EC instead of constant volume. This means you will only top it off with water in order to bring the EC back to its starting value, but you will never add nutrients to the reservoir. This will cause your total volume to drop with time as you will be adding less volume each time to get back to the original EC. When the volume drops to the point where you have less than 50% of the original volume, completely replace your reservoir with new nutrients. This gives you a better idea of how “used up” your solution really is and how close to bad imbalances in the nutrient solution you might be. A large flowering plant will normally uptake 1-2L/day, meaning that with a reservoir sized at around 5 gallons per plant, it will take you around 2-3 weeks to replace the water.
Note that more efficient and complicated ways to manage a nutrient reservoir exist, but the above is a very safe way to do so without the possibility of toxic over accumulations of nutrients from attempts to run at constant volume by attempting to add nutrients at a reduced strength to compensate for plant uptake. Topping off with nutrients without regard for the changes in the nutrient solution chemistry can often lead to bad problems. The above approach is simple and gives good results without toxicity problems.
Change your pH according to the return pH values
Instead of watering at the normal 5.8-6.2 range, check the pH of the return on a drain cycle to figure out where you should feed. Since a flood and drain system is not a constantly recirculating system, the solution conditions do not necessarily match the root zone conditions and trying to keep the solution at 5.8-6.2 might actually lead to more basic or acidic conditions than desired in the root zone. Instead, check for the return pH to be 5.8-6.2, if it is not, then you need to adjust your reservoir so that it waters at a higher or lower pH (always staying in the 5-7 range) in order to compensate for how the root zone pH might be drifting. This can take some practice, but you can get significantly better results if you base your pH value on what the return pH of your solution is, rather than by attempting to set the ideal pH at the reservoir. You will often see that you will be feeding at a consistently lower pH 5.5-5.6, in order to accommodate nutrient absorption.
Finally
The above are some simple, yet I believe critical things to consider if you want to succeed with an ebb and flow system. The above should make it much easier to successfully run a setup of this kind and grow healthy and very productive plants. Let me know what you think in the comments below!