Controlling pH in hydroponics using only electricity
The ability of plants to assimilate nutrients changes as a function of pH. This makes maintaining the pH of nutrient solutions within an acceptable range – most commonly 5.8 to 6.2 – one of the most important tasks in a hydroponic crop. This is commonly done with the addition of strong acids or bases to decrease or increase the pH when it drifts away from the intended value. This requires either manual monitoring with careful addition of these substances or automated processes using pumps to ensure the pH always remains at the correct value. However both of these methods lack fine control, require a lot of maintenance and monitoring and can lead to costly mistakes. Today I want to discuss an alternative method that relies on a completely different idea to control pH, the idea that we can oxidize or reduce water using electricity to achieve changes in pH. Yes, you can change pH using literally only electricity.
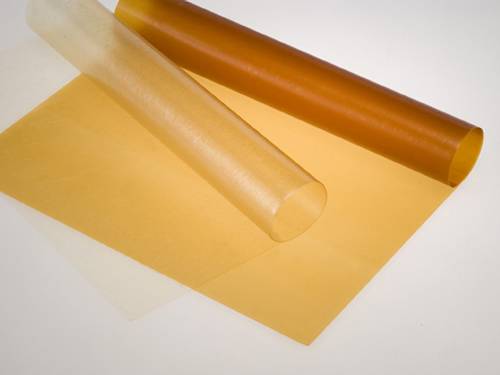
Let’s start by discussing pH and talking about how it is changes. The pH of a solution is calculated as -Log(|H+|) where |H+| is the molar concentration of H+ ions in solution. In water, the dissociation constant 1×10-14 (at 25C), always needs to be respected, so we always know that the product of |H+| and |OH–| needs to give us this number. When you add acids you increase |H+| conversely |OH–| decreases and the pH goes down, when you add bases |OH-| increases, |H+| decreases and the pH goes up. In simpler terms everything you need to decrease pH is a source of H+ and everything you need to increase pH is a source of OH–.
This is where electrochemisty gives us the simplest solution we could hope for. Water can be oxidized or reduced. When you run a current through water – above the minimum required voltage – water splits into hydrogen and oxygen molecules. In the image below you can see how the water oxidation reaction generates H+ ions while the reaction on the right generates OH- ions. When you do this in a single cell – as shown below – the H+ ions generated at the anode react with the OH- ions generated at the cathode and the pH of the solution remains neutral while oxygen is produced at the anode and hydrogen is produced at the cathode.
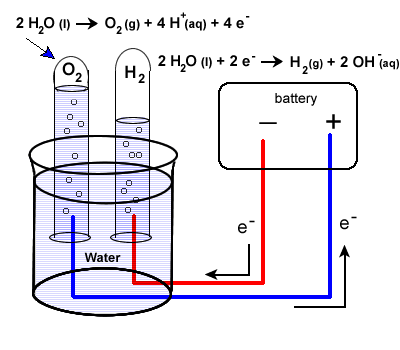
However, we can take advantage of ion exchange membranes to separate these two processes, allowing us to control where each reaction happens and where the acid or base is generated (preventing them from just mixing and neutralizing). As a matter of fact, all we need is to have an electrode in our nutrient solution and another electrode in an auxiliary cell, separated from our nutrient solution by an ion exchange membrane. This concept is actually not new and was already proposed in a 1998 paper to control pH in hydroponic systems. Although it was never tried in a production system, all the concepts were validated and were shown to perform adequately in test solutions.
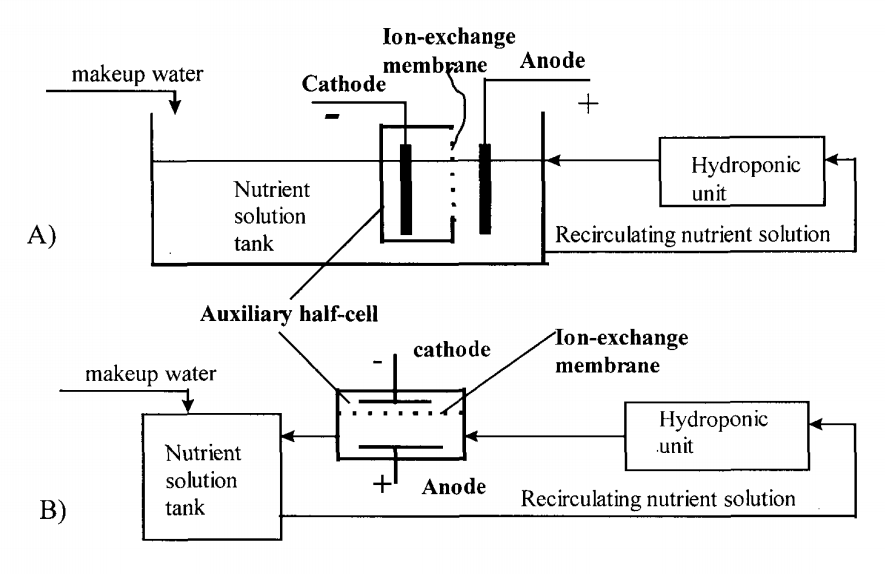
One of the big challenges of this setup is that the cathode side involves hydrogen gas evolution – which could be dangerous – but can be completely avoided by replacing the cathode’s half reaction with much more benign chemistry. As an example – also suggested in the paper above – you can replace the cathode half-cell with a copper sulfate solution with a copper electrode, with an anion exchange membrane. This would allow you to have your reduction reaction be the reduction of copper onto a copper place, which is a very tame reaction. Since the membrane only exchanges anions you would only have sulfate go to your nutrient solution, which is a benign anion in hydroponic culture. This of course means that your half-cell electrode and solution would need to be replaced with time, but this is completely independent from the control process (much more like refilling a tank of gas). The anode would only evolve oxygen in your nutrient solution, which is a potentially beneficial side effect.
Using a copper sulfate half-cell would however limit the control system to lower pH but this is not a problem since this is the most commonly used operation in hydroponics (very rarely do people have to increase the pH of their solutions). If a proper venting system or catalytic recombination system is used on the cathode side you could also go with the simple water oxidation/reduction route and be able to increase or decrease the pH using basically, pure electricity.
I am definitely planning to build one of this setups in the future. Coupled with modern sensors and micro controllers this could make it extremely easy to maintain very fine control over the pH of the solution, compensating – in real time – all the changes in pH carried out by plants without the risk of heavily over or under compensating (as it happens when you use acid/base additions).