Sugars in hydroponic nutrient solutions
Carbohydrates are an integral part of plants. They produce them from carbon dioxide, requiring no additional external carbon inputs for the process. However, since plants can absorb molecules through their leaves and roots, it is perhaps natural to wonder whether they could also get carbohydrates through the roots and avoid some of the stress they go through in order to produce these molecules from scratch. If plants can uptake sugar and we feed them sugars then will we get fruits with more sugars and bigger plants? It’s an interesting question that I will try to answer within this post, looking at the potential use of simple sugars within hydroponic nutrient solutions.
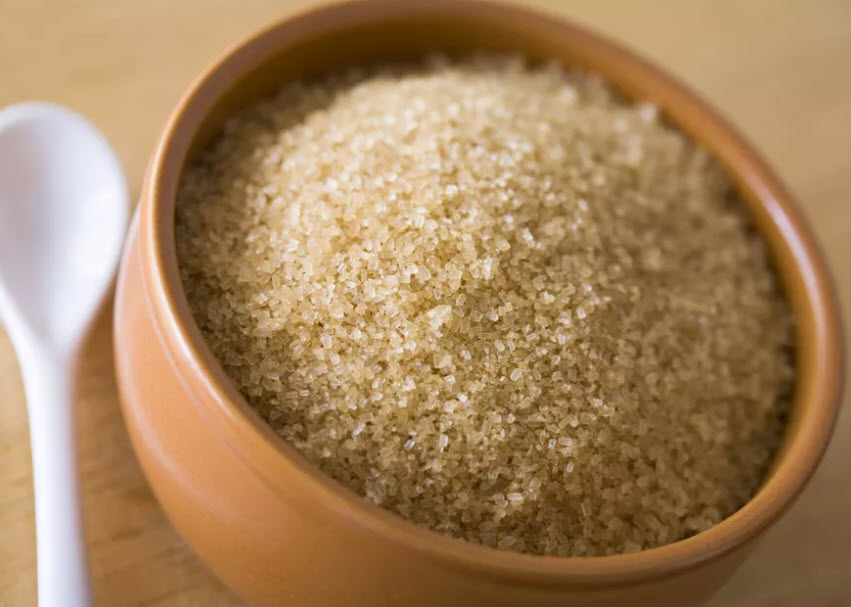
Although the above idea sounds straightforward, it hardly has any interest in the scientific literature or the commercial hydroponic industry. You will find no significant number of research papers studying the use of sugars – simple or complex – in hydroponic nutrient solutions and very few studies looking at sugar uptake and the interactions of in-vitro plant tissue with simple sugars. This lack of interest and use is no accident, it comes from an already established understanding of plant physiology and the realization that it is not cost effective, useful or needed to add sugars to nutrient solutions.
Let us start with what we know about the subject. We know that plants exude very significant amount of sugars through their root systems and we also know that they can re-uptake some of these sugars through their roots (see here). From this paper it seems that maize plants could uptake up to 10% of the sugars they exude back into their root systems, which implies that some exogenous sugar application could find its way into plant roots. Even worse, transporting this sugar up to the shoots is extremely inefficient, with only 0.6% of the sugar making it up the plant. This tells us that most of the sugar is wasted in terms of plant usage, a large majority never makes it into the plant and the little amount that makes it actually never goes up the plant. Plants are simply not built to transport sugars in this manner, they evolved to transport sugars down to roots and to fruits.
But what about the roots? Given that the plant tissue that would be in direct contact with the sugar is the roots, it is logical to think about positive effects affecting them primarily. We have some studies about the influence of sugar solutions in seedlings (like this one) which does show that sugars can stimulate the growth of new root tissue in very small plants. However in large plants most of the sugar content in the roots will come from transport from the higher parts of the plant and the local sugar concentration will be low. Seedlings can likely benefit from sugars in the roots because leaves are producing very little at this time but larger plants are unlikely to benefit from this effect.
There is however one effect that sugars have that is very clear, they feed the rhizosphere around the plant’s roots. Although plants try to care about this themselves – by exuding an important amount of sugars and organic acids – an exogenous sugar addition would most likely boost the amount of microbes around plant roots (both good and bad ones). The profile of sugars and acids exuded by plants is most likely tuned by evolution to match the microbes that are most beneficial to it and an unintended and negative effect of sugars is to boost all microbe populations at the same time, regardless of whether they are good or bad for the plant. This also increases oxygen demand around roots – because aerobic microbes will want to oxidize these sugars – reducing the amount of oxygen available to plant roots. For this reason, any application of a sugar to a nutrient solution requires the inoculation of the desired microbes beforehand, to ensure no bad actors take hold. It also requires the use of a media with very high aeration, to prevent problems caused by oxygen deprivation.
Sadly there aren’t any peer reviewed papers – at least that I could find – investigating the effect of exogenous sugars on the yields of any plant specie in a hydroponic environment. Given our understanding of plant physiology, any positive effects related with anecdotal use of sugars are most likely related with positive effects in the rhizosphere that are linked with improved production of substances that elicit plant growth in the root zone by favorable microbes. This is mainly because it is already well established that transport of sugars within plants from the roots to the shoots is incredibly inefficient, so any contribution of the roots to sugar uptake will be completely dwarfed by the actual production of sugars from carbon dioxide in the upper parts of the plant. It is not surprising that no one seems to want to do a peer reviewed study of a phenomenon whose outcome is already largely predictable from the accepted scientific literature.
If you’re interested in the use of sugars in hydroponics, it is probably more fruitful to focus on microbe inoculations instead. Sugars themselves are bound to provide no benefit if they are not coupled with a proper microbe population and, even then, you might actually have all the benefits without any sugar applications as the microbes can be selected and fed by plant root exudates themselves in mature plants although sugars might provide some benefits in jump starting these populations, particularly in younger plants. Also, bear in mind that there is also a very high risk of stimulating bad microbes with the use of sugars, especially if oxygenation is not very high.