Properly positioning temperature and humidity sensors in a hydroponic growing environment
Temperature and humidity are two key variables you need to measure. They are important because they determine how your plants will transport water, and transpiration controls a lot of processes, with nutrient transport being one of the most important ones. However, the value of these variables in a growing environment – being that a greenhouse or a grow room – can change substantially depending on where they are measured. It is therefore critical to know where to place sensors and how to interpret their readings based on their location. In this post, we are going to discuss where it is best to measure these variables and what consequences it could have if these values are not measured properly.
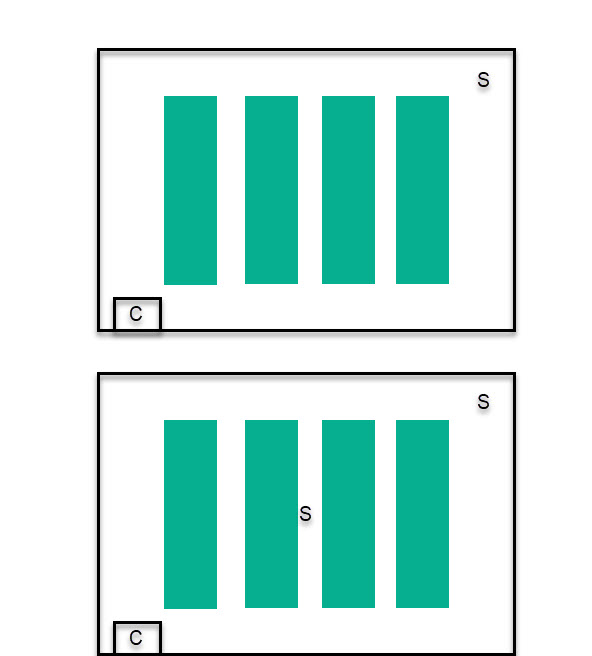
Let’s start with the worst possible case, you only have one set of sensors and you need to control your environment with it. In this case, place your temperature and humidity sensors at canopy height, as far away as possible from both the AC ducts and the humidifier/dehumidifier, make sure the sensors are hanging in the air and not stuck to a wall or tubing. Then, make sure you use a hot wire anemometer to verify that your air movement speed is at least 0.3m/s across the entire room. This setup ensures that the worst controlled part of the room is at the correct value and it also attempts to minimize the gradient created from the control sources to the sensor using a good amount of air circulation. It is not perfect though and significantly different “climate zones” will be created close to and far away from the climate control devices.
The above setup can be used effectively in small growing environments, but can be problematic as both the number of plants and the size of the growing environment increases. At this point, using a single set of sensors is not an option if adequate climate control is desired. In these cases, multiple sensors need to be placed to ensure that climate control is being done properly. When using multiple sensors, place the second sensor at the place with the lowest air circulation inside the room, at canopy height, which is usually in the middle of the room, then place subsequence sensors as far away from either this or the first sensor in sequence. When doing climate control, the system needs to ensure all of the sensors remain within a “safety band”, making sure no sensor becomes too cold/hot, humid/dry, during control cycles.
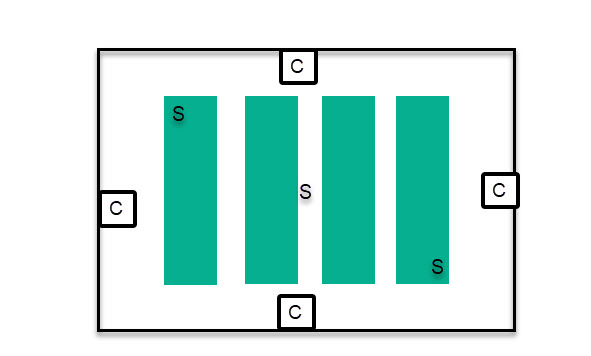
When you implement a sensor system like this, you will realize pretty quickly that climate becomes very hard to control in a larger room when there is only one source of control (one AC, one humidifier, and one dehumidifier) because gradients become too big for effective control, so it takes too long for the AC to be able to properly control the room while ensuring all sensors remain within proper boundaries. In this case, it becomes necessary to add multiple sources of control, so that the extent of gradients within the room can be minimized. This means adding multiple ducts for the output of an AC, multiple humidifier/dehumidifiers, etc.
In these cases, sources of control are placed outside of the plant canopy to avoid plants being exposed to the flows from these control sources (which would expose them to very cold/hot/dry/humid air). Then the sensors need to be placed within the plant canopy, starting from as far away as possible from all sources of control – usually the middle of the canopy – and then to the corners of the growing environment.
Note that the control algorithm needs to ensure all of these sensors are within the proper control band and not attempt to control the average reading of these sensors. If you try to use the average of sensors to control a room, you might be left with a room where two extremes are present and the control system believes everything is ok while these extremes are maintained. The median is a better way to control a room, but it only becomes useful when 5 or more sensors are used. If only 2 or 3 sensors are used, ensuring all of these sensors are within adequate bands is fundamental to ensure that the room will have a lower chance of having humidity/temperature microclimates that will be detrimental to plant growth.