Can you use regular soil fertilizers in hydroponics?
If you have just started your journey into hydroponics you’re probably wondering why you need to spend your money in hydroponic specific nutrients when there are so many cheaply available soil fertilizers sold out there. Certainly there are all plant food and there must be some way you can use all these cheap soil fertilizers to create a suitable replacement to feed your hydroponic crop. In this post I want to explain some of the key differences between hydroponic and soil fertilizers, when soil fertilizers can be used in hydroponics, how they can be used and when it is definitely a bad idea to try to use them.
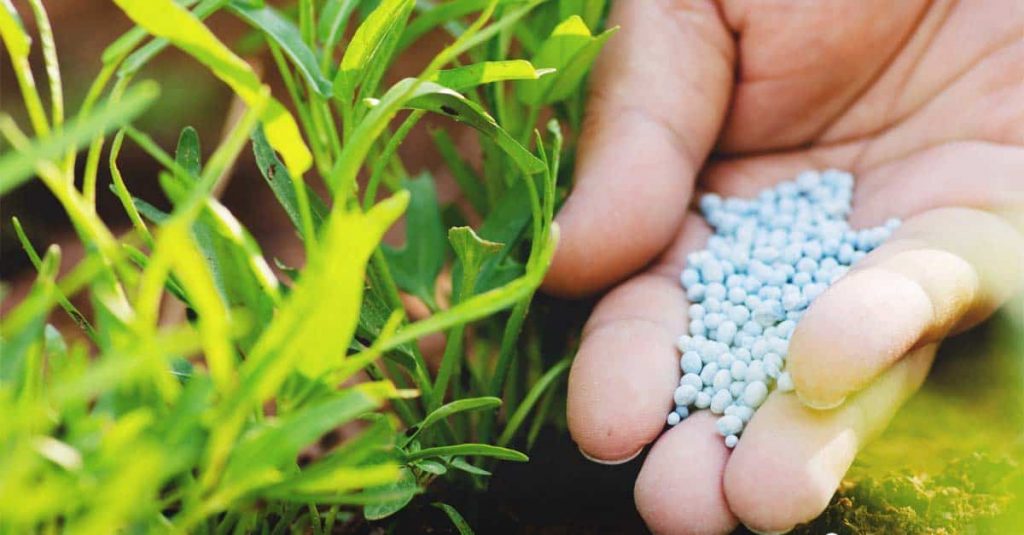
To understand the difference between soil and hydroponic fertilizers we must first understand the difference between both growing setups. In hydroponics we try to grow plants in sterile and chemically neutral supporting media where all the nutrients are expected to be provided by the nutrient solution while in soil the media is not intended to be inert – it contains organic matter, minerals that can dissolve and living microbes – and we expect some of these to provide nutrition to our plants. Fertilizers for soil are intended to aid this process – provide material for microbes to process and supplement some of the lacking elements in the soil – while hydroponic fertilizers intend to provide all required nutrition in the forms that are mostly favorable for plants. Fertilizers for soil are often also meant to be applied once or very occasionally, while fertilizers for hydroponics are expected to be fed to the plant very frequently.
In chemistry terms, this means that fertilizers for soil will tend to contain forms of nitrogen that can be processed slowly by microbes in soil – urea and ammonium salts – while hydroponic fertilizers contain mostly nitrate salts. It is rare for soil fertilizers sold to home growers to contain large amounts of nitrates because these are easily washed aware by rain, are strong pollutants of underwater ground sources and are only shortly available for plants due to their high mobility in soil. However ammonium and urea are a terrible idea in hydroponics since ammonium fed frequently strongly acidifies the media and plants supplied their nitrogen only from ammonium in solution will tend to show toxicity issues quickly. Soil fertilizers rely on bacteria to convert this ammonium and urea to nitrate in a slow process, hydroponic fertilizers do not, they contain nitrate which is the final form of nitrogen that plants prefer for healthy growth.
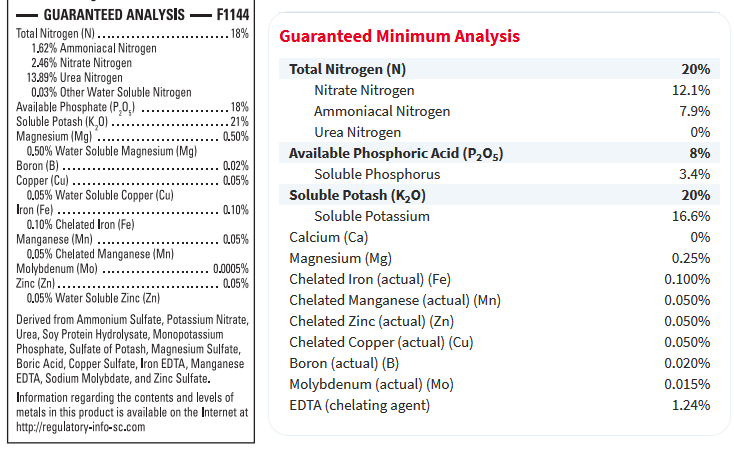
The image above shows you a comparison between the labels for a water soluble soil and hydroponic fertilizer. In terms of NPK they both seem to be similar fertilizers, but the hydroponic fertilizer will have most of its nitrogen as nitrate while the other fertilizer has most of its nitrogen as urea. There are some other differences, mainly that the amount of phosphorous in the soil fertilizer is more than double that of the hydroponic fertilizer, which is also common given that phosphate is fixed rapidly in soil and therefore a higher excess is often added to ensure plants get enough supply. At an application of 1g/L the soil fertilizer would provide 75+ ppm of phosphorous while the hydroponic one would provide around 35. Also note that none of these two fertilizers would be enough to provide total plant nutrition since they both lack a source of Ca, which is commonly provided via a separate product in both cases.
So can any soil products be useful in hydroponics? Yes. First you need to completely avoid products that contain N mainly as urea or ammonium. Useful products to get for your hydroponic grow will be fully water soluble and will either contain nitrogen solely as nitrate or no nitrogen at all. A very coarse DIY formula can usually be put together using something like a micro nutrient containing 0-10-10 bloom fertilizer (which contains no nitrogen) coupled with a source of nitrate, like agricultural grade calcium nitrate. You can use Hydrobuddy – my open source hydroponic nutrient calculator – to figure out the nutrient contributions of each one of the products you decide to get or have easily available and create an acceptable formulation from their use. The program also contains a long list of readily available raw salts that you can use to make your own fertilizer formulations from scratch if you wish to do so.
In the end, soil products for home growers are not designed for hydroponics use and should therefore be avoided except as a last resort if raw salts or hydroponic specific nutrients cannot be purchased. If you’re interested in saving money, learning how to prepare your own fertilizers from raw salts will always be the best and cheapest option, provided you have the time and desire to learn how to do it properly.