Five common misconceptions around nutrient management in hydroponics
After many years of experience as a consultant in the hydroponic industry and interacting with dozens of different customers growing different plants with different systems, there are some common misconceptions that become apparent as time goes by. As a chemist, the ones I remember the most are related with the management of nutrient solution and the diagnosis and treatment of nutritional problems in plants. In today’s post, I want to talk about some of these misconceptions and hopefully shine light into what the more accurate interpretation of these phenomena actually is.
The EC is increasing, my plants are not feeding! One of the concerns I most commonly address is that plants are “not feeding” because the electrical conductivity (EC) of the nutrient solution is not decreasing, but actually increasing after the solution goes through the plants. Many growers think that EC measures nutrients in a solution, so if a plant feeds on nutrients, then the EC should naturally decrease as the plant feeds. This is wrong because the plant consumes both nutrients and water and EC is a proxy for nutrient concentration and not for the absolute amount of nutrients in the water. As a plant feeds it will absorb both nutrients and water but significantly more water than nutrients. Remember, plants are mostly made out of water and also use water to regulate temperature, humidity and nutrient uptake, so they will take way more water than nutrients, increasing the EC as they feed. As a plant grows larger it’s nutrient and water demands grow, but the water demand grows significantly more than the mineral nutrient requirements, meaning the plant will progressively increase the EC more and more as it feeds more and more aggressively.
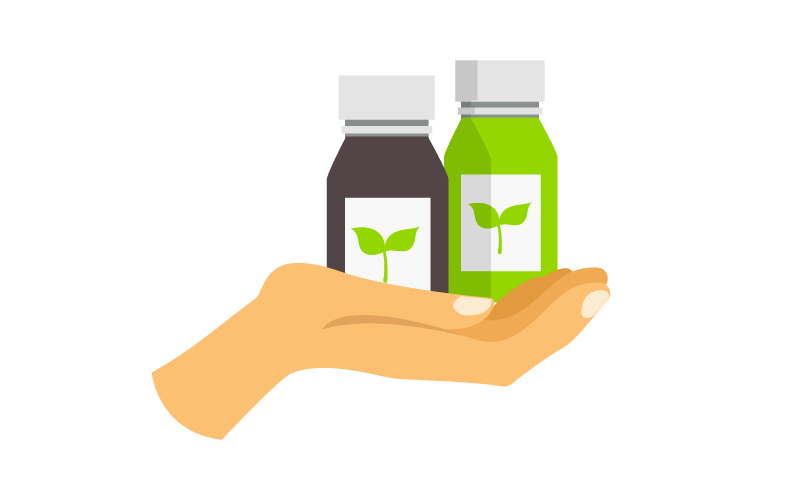
The plants are yellowing, there must be a nutrient deficiency. As soon as plants start to show signs of yellowing, a significant amount of growers will immediately look and try to interpret this as a sign that there is some form of nutritional deficiency. Most that subscribe to this belief will look for pictures of deficiencies online and do their best to match what they see with a deficiency and then proceed to supplement the solution with some fertilizer that contains the “missing element”. More often than not, this is actually not caused by the composition of the solution at all but by some environmental factor that is not being properly managed. In run-to-waste systems this is most commonly related with a significant pH drift in the media – reason why it is always necessary to measure pH/EC of the run-off – but it can also be related to unnecessarily harsh VPD conditions or even a lack of enough air circulation. I would say that 5/10 times, problems with the plants have virtually nothing to do with the nutrient solution at hand.
If you want more X, then increase X in the nutrient solution. The relationships between the concentration of elements in a solution and the concentration of nutrients in plant tissue is not linear. Sometimes, increasing the concentration of an element in solution can actually lead to less of that nutrient being present within plant tissue. An example of this can be phosphorous, a plant can suffer from a phosphorous deficiency due to the formation of insoluble iron phosphate compounds in tissue that appear when the concentration of these two elements goes above some threshold. As more of either is added, more of these insoluble compounds are formed and less of P and Fe actually gets to the plant. Another example can be Ca, where the amount of Ca in tissue is more dependent on VPD than on the concentration of Ca in solution, changing the VPD by 20% will affect Ca in tissue significantly more than adding 20% more Ca to the solution in some plant species. In these cases you might add 20% more Ca but your VPD drops 20% and you actually see a decrease of Ca in tissue. Sadly nutrient dynamics are not simple and often a more holistic picture needs to be used to approach nutritional management!
Plants need aggressively more phosphorous when they flower. Most commonly used fertilizers in soil tend to have higher P/K values when they target “flowers”, this is because, in soil, phosphorous is not highly available and the supplementation of highly available phosphorous during flower can be very useful to plants. However, flowering plants in hydroponics always have access to significant amounts of soluble P and most actually do not require an increase from this base level when they go into their flowering periods. Many commercial hydroponic solutions used for tomatoes will – for example – keep their P values at 50 ppm through the entire growing period, only increasing K during the flowering period, but not P. Experiments across various commercially grown flowering species have shown that levels in the 50-65ppm range are ideal for many plants during their entire life cycle, this matches the experience of growers in the horticultural hydroponic industry.
There is a perfect nutrient solution. Many growers go on a “holy grail” quest to find the “perfect” nutrient solution that will give them the absolutely best yields. Many commercial fertilizer producers also call me asking to formulate “the best possible formulation” to grow a given type of plant or – even worse – to grow a wide variety of plants. The truth is that the ideal solution to feed a plant will depend on the genetics, the environment, the irrigation system, the growing media, etc. Due to the large amount of variability between growing setups, plant genetics and growing methodologies, more often than not, the nutrient optimization process needs to be carried out for every grower. Don’t get me wrong, a base formulation will probably get you 80% of the way to your maximum potential yields – nutrient solutions are not miracle generators, they are just food – but conquering that final 20% will require a lot of additional effort that will most likely be limited to your particular conditions. This is because most environments are limited by different factors and using the nutrient solution to help overcome some of these limitations will modify the solution in a way that’s probably detrimental for other environments.
I hope the above misconceptions show that the world of nutrient solutions and plant management is not so simple and that there is a lot that goes into understanding how nutrients interact within a plant and how a given growing environment needs to be modified in order to improve crop results. My goal is to help you expand your knowledge about hydroponics and better reach your goals by overcoming some of these misconceptions and tackling some of the true problems within your hydroponic crops.