Disinfection of nutrient solutions in recirculating hydroponic systems
Plant growing systems that recirculate nutrients are more efficient in terms of fertilizer and water usage than their run-to-waste counter-parts. However, the constant recirculation of the nutrient solution creates a great opportunity for pathogens and algae to flourish and colonize entire crops, with often devastating results. In this post, we are going to discuss the different alternatives that are available for disinfection in recirculating crops, which ones offer us the best protection, and what we need to do in order to use them effectively. I am going to describe the advantages and disadvantages of each one so that you can take this into account when choosing a solution for your hydroponic crop.
Disinfection of recirculating nutrient solutions has been described extensively in the scientific literature, the papers in the following links (1,2,3,4) offer a good review of such techniques and the experimental results behind them. The discussion within this post makes use of the information within these papers, as well as my personal experience while working with growers all over the world during the past 10 years.

In order to kill the pathogens within a hydroponic solution, we can use chemical or non-chemical methods. Chemical methods add something to the nutrient solution that reacts with the molecules that make up pathogens, killing them in the process, while non-chemical methods will add energy to the nutrient solution in some form or filter the solution in order to eliminate undesired microbe populations. Chemical methods will often affect plants – since the chemicals are carried away with the nutrient solution – and require constant adjustments since the levels of these chemicals within the nutrient solutions need to be controlled quite carefully.
Chemical methods include sodium hypochlorite, hydrogen peroxide, and ozone additions. From these choices, both hypochlorite and hydrogen peroxide have poor disinfection performance at the concentrations tolerated by plants and are hard to maintain at the desired concentrations through an entire crop cycle without ill effects. Ozone offers good disinfection capabilities but requires additional carbon filtration steps after injection in order to ensure its removal from the nutrient solution before it contacts plant roots (since it is very poorly tolerated by plants). Additionally, ozone sterilization requires ozone sensors to be installed in the facility in order for people to avoid exposure to high levels of this gas, which is bad for human health. In all of these cases, dosages can be monitored and controlled to a decent level using ORP meters, although solely relying on ORP sensors can be a bad idea for substances like hypochlorite as the accumulation of Na and Cl can also be problematic.
The most popular non-chemical methods for disinfection are heat treatment, UV radiation, and slow sand filtration. Slow sand filtration can successfully reduce microbe populations for fungi and bacteria but the slow nature of the process makes it an inadequate choice for larger facilities (>1 ha). Heat treatment of solutions is very effective at disinfection but is energetically intensive as it requires heating and subsequent cooling of nutrient solutions. For large facilities, UV sterilization offers the best compromise between cost and disinfection as it requires little energy, is easy to scale, and provides effective disinfection against a wide variety of pathogens if the dosage is high enough. It is however important to note that some UV lamps will also generate ozone in solution, which will require carbon filtration in order to eliminate the ill effects of this chemical. If this wants to be avoided, then lamps that are specifically designed to avoid ozone generation need to be used.
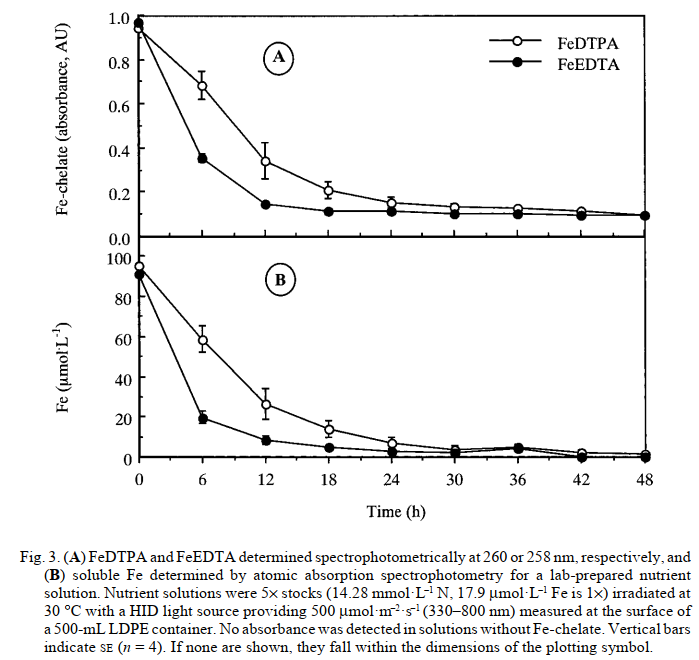
If you want to use UV sterilization, you should carefully consider the power of the lamps and the flow rate needs in order to ensure that you have adequate sterilization. Most in-line UV filters will give you a flow rate in GPH at which they consider the dosage adequate for disinfection, as a rule of thumb you should be below 50% of this value in order to ensure that the solution is adequately disinfected as some pathogens will require radiation doses significantly higher than others. You can also add many of these UV filters in parallel in order to get to the GPH measurement required by your crop. UV sterilization also has a significant effect on all microbe populations in the environment (5) so consider that you will need to inoculate with more beneficial microbes if you want to sustain microbe populations in the plants’ rhizosphere.
With all these said, the last point to consider is that both chemical and UV sterilization methods will tend to destroy organic molecules in the nutrient solution, which means heavy metal chelates will be destroyed continuously, causing precipitation of heavy metals within the nutrient solution as oxides or phosphates. As a rule of thumb, any grower that uses any method that is expected to destroy chelates should add more heavy metals routinely in order to replace those that are lost. To calibrate these replacements, Fe should be measured using lab analysis once every 2 days for a week, in order to see how much Fe is depleted by the UV process. Some people have tried using other types of Fe chelates, such as lignosulfates, in order to alleviate this issue as well (6).