Using a biodegradable iron chelate (IDHA) in hydroponics
Chelates are a very important part of hydroponic nutrient solutions as they provide a reliable source of heavy metals. Without chelates, heavy metals can easily go out of solution and become unavailable, either because they precipitate as an insoluble salt or because they are captured by active surfaces with a high affinity for metals. Among the heavy metals, Fe is the most important to chelate as it’s usually present in the largest concentration and is the most easily taken out of solution by the factors mentioned above.
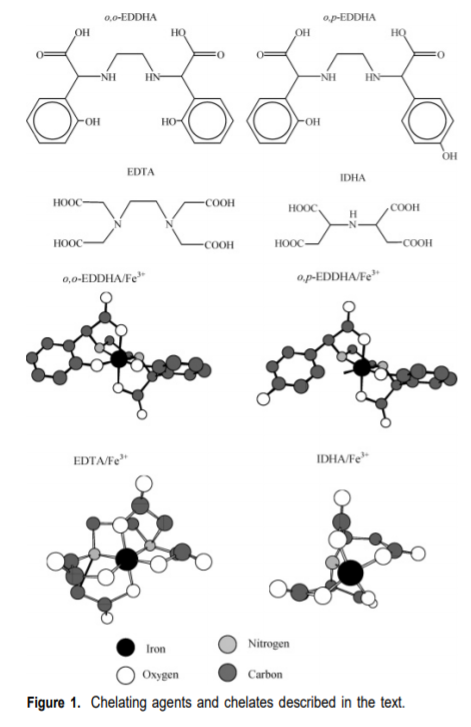
Commonly chelating agents such as EDTA, DTPA and EDDHA are used in solution and they do a great job in providing adequate supplies of micro nutrients to plants. These three chelators have a very high affinity for Fe and therefore ensure that Fe will remain in solution and available to plants. However, a problem all of these chelating agents share is their lack of biodegradability, they all enter plant tissue and are going to be very difficult to get rid of by the plant. They can therefore accumulate in plant tissues to some extent and can cause problems of their own.
There are however some chelating agents that are both effective at protecting the heavy metals and easily biodegradable, from these, the most largely studied is perhaps imidodisuccinic acid (IDHA) whose structure is showed and compared with the other chelates in the image above. Although this chelating agent shares some common structural features with traditional chelating agents its chemical structure makes it incredibly easy to biodegrade and therefore a nice candidate for fertilizer use.
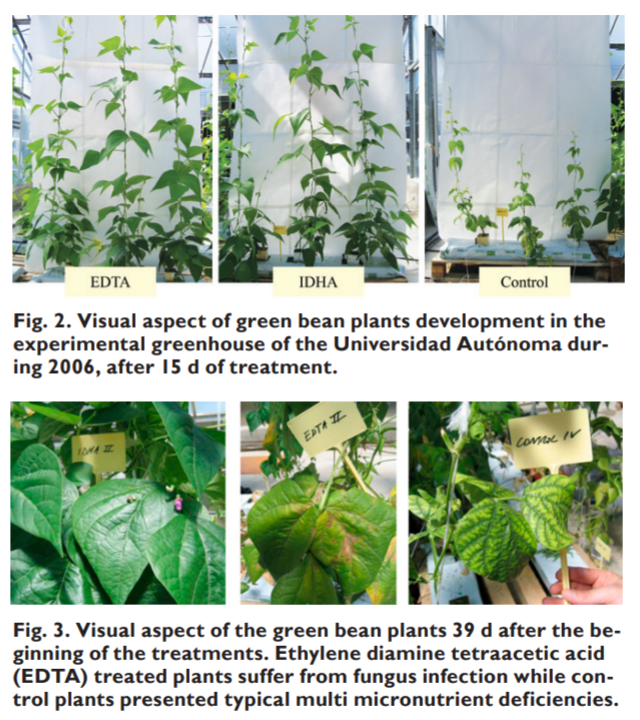
Several papers have compared IDHA fertilization to traditional Fe chelates (here, here, here, here). Although the IDHA is usually less stable in solution – as it would be expected given its chemical nature – it tends to give better results in terms of absorption and fertilization compared with the other Fe chelates. Given that it is also completely non-toxic to the plants – while the other chelates make the plant deal with the non-biodegradable aspects – plants fertilized with IDHA can actually be healthier. The image above, showing a comparison with EDTA – shows how the IDHA plants were not affected by a fungal infection that ended up affecting the EDTA treatment.
This does not mean that IDHA is the natural best choice for an Fe chelate. Some of the above studies have shown that IDHA can easily be captured by some media and its lack of stability implies that it is not a good choice for extended use in recirculating systems. However IDHA can be a better choice if the media used allows for it and the grower is able to apply it with its biodegradable nature in mind or if the desired products needs to be free of traditional chelate contaminants. In some cases – as mentioned before – it can actually be a significant improvement over traditional chelates.