Common questions about silicon in nutrient solutions
Introduction
We know that silicon can be a very beneficial element for many plant species (see some of my previous posts here and here). It mainly enhances disease resistance and increases the structural integrity of plant tissue. Because of these advantages, you will want to add silicon to your nutrient solution. However, there are a lot of misconceptions and questions about the use of Si in plants and the exact form of Si that you should use. In this post I am going to address some of the most common questions about silicon sources and how to use them properly.
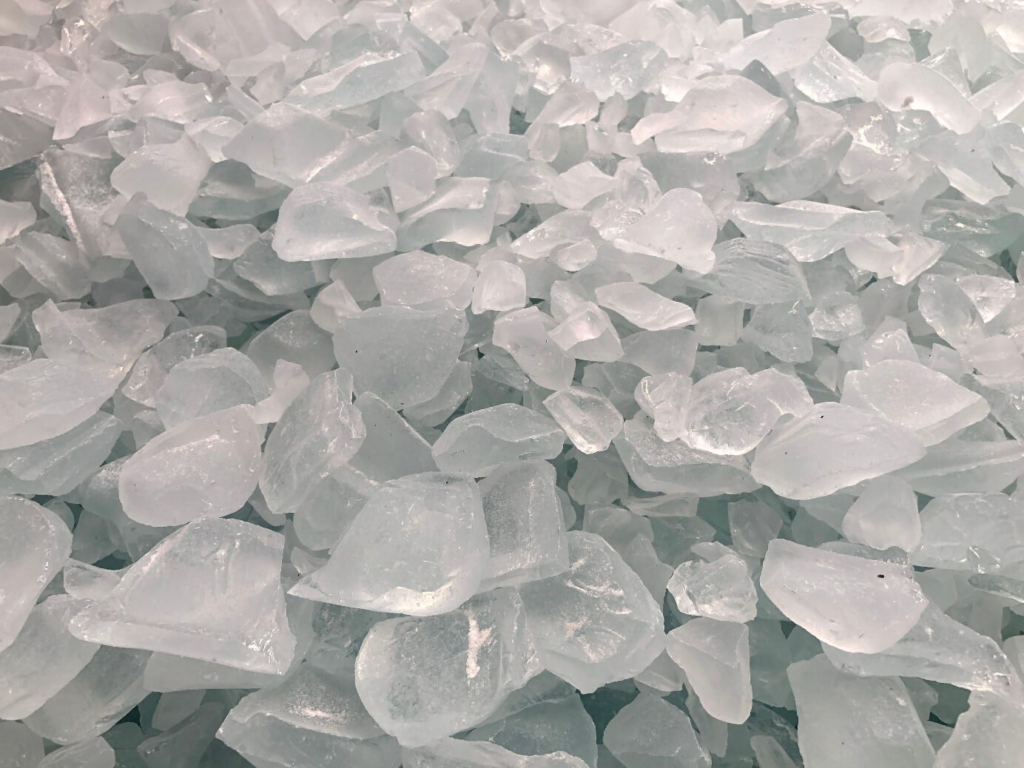
What sources are available?
To use silicon in nutrient solutions, we will generally have 3 types of sources available.
First, we have basic potassium silicates, which are solids or solutions derived from the reactions of silica with potassium hydroxide. In this category you have popular products like AgSil 16H and liquid concentrates like Growtek Pro-Silicate. These products have a very basic pH.
Second, we have acid stabilized silicon products. These are products like PowerSi Classic and OSA28. These products are always liquids and contain monosilicic acid in an acidic environment, with stabilizing agents added to prevent the polymerization of the monosilicic acid.
Third, we have non-aqueous products with organosilicon reagents, like Grow-Genius. These products do not contain water and are derived from reagents like TEOS (tetraethyl ortho-silicate) and other Si containing compounds, mainly Si containing surfactants. They are not in forms that are plant available but will generate these forms when in contact with water.
Do potassium silicates contain “less available” silicon?
When you dissolve a potassium silicate at high concentration, it forms silicate oligomers. These are large silicon chains that get stabilized in basic solutions because of their high negative charge. This is why you can create highly concentrated potassium silicate solutions in basic pH. As a matter of fact, making the solutions more basic with added potassium hydroxide often enhances the solubility of potassium silicate solids like AgSil16H (see here for a procedure on how to do this). However, when the molar concentration decreases the silicate hydrolyzes into monomeric silicate anions.
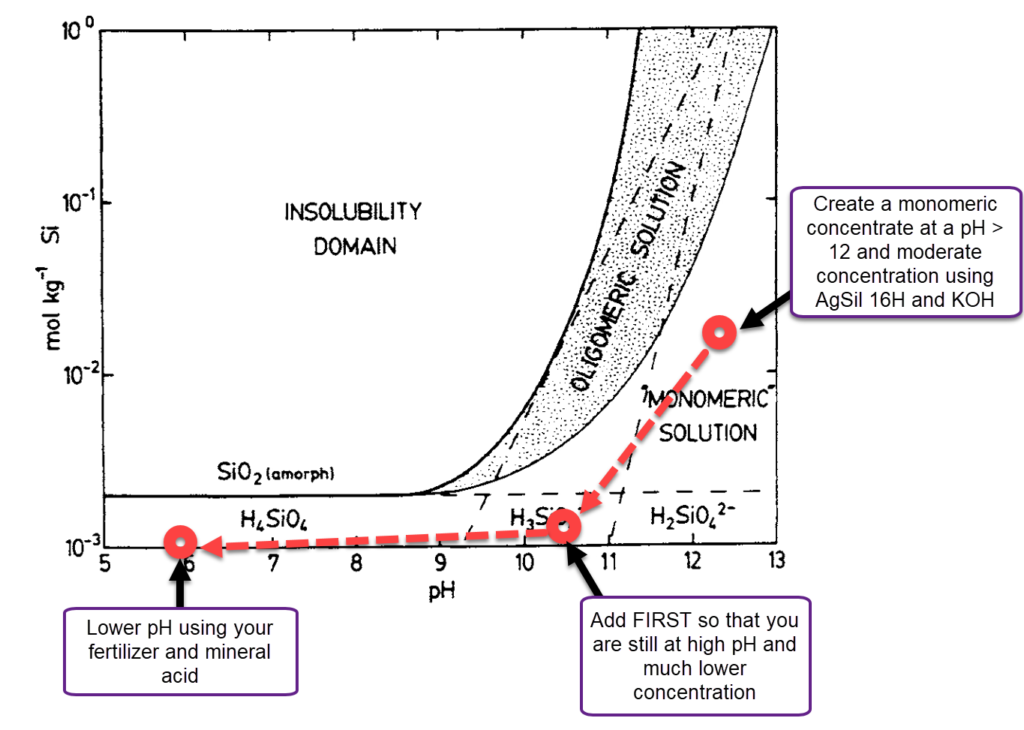
When potassium silicate is diluted in nutrient solutions, this is exactly what happens. The reduction in concentration hydrolyzes the Silicates into monomers. If the solution pH is then lowered, the final form present will be monosilicic acid. If you properly prepare a nutrient solution with potassium silicate, the end form will be monosilicic acid, the form that is mostly available to plants.
It is a misconception that potassium silicates are somehow less “plant available”. They end up producing monosilicic acid and being perfectly available, when used properly.
How do I properly use a potassium silicate?
First, if using a solid, you need to prepare a stock solution no more concentrated than 45g/L. The recommendation with AgSil 16H would be to prepare a stock solution at 15g/gal and then using this solution at a rate of 38mL/gal of final solution (injection rate of 1%). To increase the stability of your AgSil 16H concentrate you can add 1g/gal of KOH. The end addition to your solution will be +9.8ppm of Si as elemental Si and +11.55ppm of K. The KOH addition and low 15g/gal concentration ensures that silicate will already be largely present as monomeric silicate anions.
Second, make sure to add this solution to your water first. If you add this solution after nutrients, the Si will come into contact with Ca and Mg in its concentrated form, which will cause problems with its stability in solution. Add it first, then add your lowest pH fertilizer concentrate, then your Ca containing concentrate, then finally decrease the pH with an acid to the desired level if needed.
This procedure ensures you get a final solution containing monosilicic acid that will be stable. If you increase the Si in the stock solution, change the injection order, or increase the Si in the end solution beyond 20ppm of Si as elemental Si you might end up with precipitated and unavailable Si forms.
Why would you use acid-stabilized Si products?
Acid stabilized silicon sources are not more plant available. However, their starting pH is usually low and their mineral composition can also be minimal (depending on the preparation process). This means they can lower the need for acid additions and can help lower the pH of hard water sources when used. They can also contain stabilizing agents that could be beneficial for plants. However, the exact stabilizers used and the exact mineral composition used will vary substantially by product, since there are a wide array of choices available to manufacturers.
In the end, at the pH where plants are fed, acid stabilized Si and potassium silicate sources generate the exact same monosilicic acid. Plant availability is not an advantage of using this sort of product.
Why would you use non-aqueous Si products?
These products can be much more highly concentrated than either basic silicon or acid stabilized liquid silicon products by mass. This is because they are made from Si forms that are highly stable under water-free conditions. This means you can buy a small amount and add a small amount to your reservoir per gallon of solution prepared. Another advantage is that they are pH neutral and do not alter the pH of nutrient solutions at all. The formation of the silicic acid from these products requires only reactions with water, so no mineral addition, stabilizer additions or pH modifications happen.
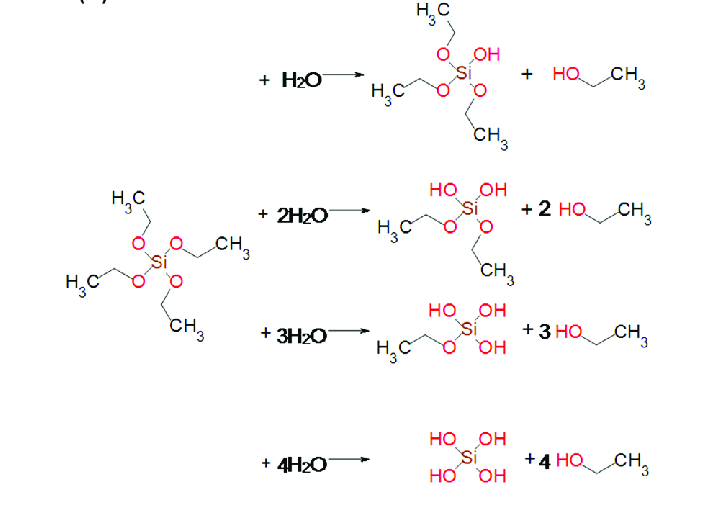
A significant point however is that the reaction of a product like TEOS with water releases other substances into solution. For each 10 ppm of Si as elemental Si that you add from TEOS you will in fact be adding ~66pm of ethanol to your solution. These alcohols can be very detrimental for root and plant growth, reason why the use of these non-aqueous Si products needs to be carefully considered. When using a product containing non-aqueous Si sources, it’s important to consider that these substances can accumulate in your root zone and may cause problems. Which organics are present and whether they will cause problems will depend on the exact formulation. When using these organosilicon sources, passing the nutrient solution through a carbon filter to remove these organics before contact with plant roots would be ideal.
Is the final Si in solution from any product type more stable?
No, all three types of products, when used properly, will end up as stable monosilicic acid in your solution. The stabilizing agents in acid-stabilized products will be so dilute that any additional stabilizing effect will be relatively non-existent. If Si is dilute enough (<20ppm of Si as elemental Si), then it will be stable in solution indefinitely (I measured 5 weeks with no changes in concentration). At higher Si concentration, the Si will tend to polymerize (no matter which source it comes from) which will create problems with stability. To have stable Si in solution make sure that you prepare it properly and that you keep the concentrations low enough.
If they are mostly the same in terms of Si availability, why do I see differences between different products at an equivalent Si application rate?
Despite all of the different Si products leading to the same form of Si in the final solution, acid-stabilized Si products will contain a wide array of additional substances that are going to be active nutritionally. For example, Boron and Molybdenum are very commonly used stabilizing agents. Products, like PowerSi bloom, also contain “exotic plant extracts” (according to their website). Commonly used stabilizing agents include glycerol, carnitine, choline and sorbitol. All of these could potentially have an effect on the plants at the concentrations added with these products. Some of these stabilizing agents are usually added at 10-50x the amount of Si present by mass, meaning that your Si supplement might be adding way more of these stabilizing agents than what you’re adding in terms of Si.
What product is more cost effective per delivered mole of monosilicic acid?
There is a lot of space in labeling regulations to allow fertilizer manufacturers to trick people into believing a product might be more concentrated or dilute than another. First of all, labeling a product as “% of monosilicic acid” does not mean that the product contains that percentage of monosilicic acid, it means that the product contains Si, such that if that silicon was all converted to mono-silicic acid, it would give that percent. The only products that contain monosilicic acid in its actual form from the start are acid-stabilized Si containing products, which are usually limited to low concentrations due to the reactivity of this molecule when present.
Both non-aqueous silicon products and soluble potassium silicate products contain precursors to monosilicic acid. One in the form of organosilicon compounds and the other in the form of silicate chains. As mentioned above, both precursors can lead to very high conversions to mono-silicic acid when properly used.

To compare the actual concentration of products, it is best to always convert the amounts to elemental Si percentage values. To convert monosilicic acid % values to Si, multiply the value by 0.2922, to convert SiO2 values to Si, multiply the value by 0.4674. For example, 40% Si as monosilicic acid is equivalent to 11.68% Si as elemental Si. Soluble potassium silicates like AgSil 16H can be around ~24% Si as elemental Si by mass, making them the most highly concentrated and lowest cost form of bioavailable silicon when used properly. More highly soluble potassium silicates than AgSil16H will usually be lower in Si, as higher K proportions lead to better solubility and a lesser need to add KOH when preparing stock solution. The table above, showcases the price differences per gram of Silicon of different products as of Jan 2023. When purchased in bulk (50 lbs) AgSil16H can be up to two orders of magnitude lower cost than other alternatives.
I have done lab tests measuring molybdenum reactive Si that show all the Si in AgSil16H can be quantitatively converted to monosilicic acid when following the preparation guidelines mentioned in this post.
What is your recommendation?
After studying the subject for years, using different products with different growers and testing the chemistry myself (preparing stabilized silicic acids and measuring active Si concentrations). Given the price of Si products and the chemistry involved, I would suggest anyone interested in Si supplementation in nutrient solutions to use a potassium silicate solid product. I would suggest to prepare a suitable stock with potassium silicate and potassium hydroxide to increase pH and stability and then prepare their nutrient solutions from dilutions of this stock. If a solid product like AgSil 16H is not available, then using a basic silicate concentrate product would be the next best choice. Usually preparing a more dilute stock from these products is recommended to ensure the stock already contains monomeric silicate.
I don’t think acid-stabilized silicon products or non-aqueous Si products are worth the price premium. If you’re having better results with a non-potassium silicate product compared to potassium silicate, bear in mind that this is likely because either the potassium silicate stock preparation and dilution were not done correctly or the product you’re using contains a substance different from Si that is giving you those effects. The stabilizing agents themselves are going to be much lower cost, so testing the eliciting effects of these agents might be more economical for you than using these expensive products long term.
In cases where mixing stocks and handling basic reagents is problematic or there is limited availability to adjust pH, then the use of non-aqueous Silicon reagents might be desirable. Non-aqueous silicon forms are also the most robust to mixing errors – wrong mixing order, mixing at variable pH, etc – because the hydrolysis reactions happen readily under a wide variety of conditions. However, my recommendation is to always couple these with carbon filtration to avoid potential issues from their organic side-products.
If you have issues with the use of soluble silicon sources – because of your initial water composition, injector limitations, cost, etc – and your media supports amending, I would also suggest considering using solid amendments to supplement Si (watch this video I made for more information). Amending can be a great choice, much more economical than soluble Si supplementation.