Why are different hydroponic formulations required for different situations?
Hydroponic growers tend to have very different experiences with nutrient solutions. It is not uncommon to find a grower who “swears” by product A and another who says product A delivers terrible results but product B is “the best”. This causes a lot of confusion among new growers since there doesn’t seem to be any agreement about what the “best formulation” is. Shouldn’t we know by now what the “best nutrients” are? Given how many crop cycles are grown each year and how many iterations growers go through, you would think it would be only a matter of time before we know for certain how to create the “perfect recipe” to maximize yields and minimize problems and diseases. Why haven’t we achieved an optimal formulation for each plant species? The answer, is that nutrition is not only about nutrients and optimal nutrients are only optimal for a very specific set of conditions.

Commercial hydroponic fertilizer manufacturers would want you to believe that they have figured it out. They have a given set of formulations for people using Coco, another for people using rockwool, some for hard water, some for soft water, a whole array of different products to choose from where you will certainly find one that suites your needs if you just follow their guidelines. However, these different products are formulated using very broad assumptions, for example that the Coco you use required initial pretreatment with Ca salt or that your input water will contain substantially large amounts of Ca and Mg, because it’s a “hard water” formulation.
Commercial products are also often made with implicit assumptions that depend on the experience of the people formulating the nutrients. For example a nutrient manufacturer might formulate nutrients that delivered excellent results while working at high VPD conditions, without realizing this was even the case. Another might formulate nutrients for the entire opposite case. A person testing a product might also like to only irrigate to a small amount of run-off, while another will irrigate till a large amount of run-off is collected. All these things affect the concentrations of nutrients the plants are exposed to, because they fundamentally affect the amount of water that the plants have access to and the transpiration demand the plant is subjected to.
This is why a grower might swear by a given nutrient formulation and be completely right in that it delivers amazing results, while another will find this formulation just gives mediocre results with a bunch of nutrient deficiencies. The temperature, humidity, media, irrigations per day, irrigation volumes, input water composition and nutrient ratios, all play a role in determining whether the plant is able to properly uptake nutrients and whether these nutrients are ideal for this case. I’ve seen a person using a low K, low Ca formulation for rockwool with pretty limited irrigations be quite successful with it, while another using the same formulations under high irrigation volumes had substantial problems. The first person was relying on large dry-backs to increase oxygenation and increase nutrient concentrations to a point that suited the plants very well, the second person failed with this formulation because nutrient concentrations were too low and were never able to reach the same values they reached for the first one with increased irrigation volumes and frequencies.
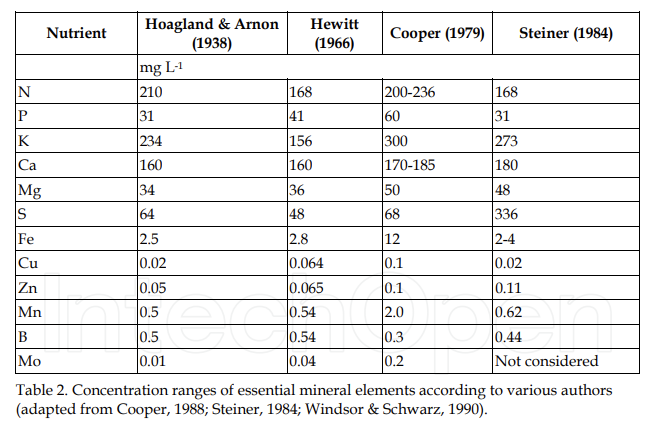
The development of an optimal formulation for a hydroponic crop is therefore a long process that needs to be guided by a considerable evolution from a given “good guess” base towards what is optimal for the specific conditions. More often than not, the formulation will be optimized alongside some constraints – like those dictated by climate control and light providing abilities – and will therefore be pretty tightly bound to the particular environment. My advice is to start from a good guess base, using the knowledge about the chemistry of the environment – input water, media – and to evolve that base using tissue analysis and crop yield results in order to achieve better and better results. Finding an ideal nutrient solution can take a lot of time and effort but it can substantially increase yields and improve quality levels.