Kinetin, a powerful hormone for flowering plants
Kinetin was the first cytokinin ever discovered. Scientists have used it extensively to stimulate cell division in tissue culture, as it is a powerful growth hormone. However, there isn’t a clear understanding of the effects of kinetin in large flowering plants, reason why it hasn’t been widely used as an additive in plant culture. In this post, we are going to take a look into the practical application of kinetin. We are going to look into published research and discuss whether kinetin could be used to enhance plant yields. I will refrain from discussing the history and chemical structure of kinetin, for a basic introduction about kinetin and its history, I suggest reading this paper (1). I will also use some information contained in this review (5).
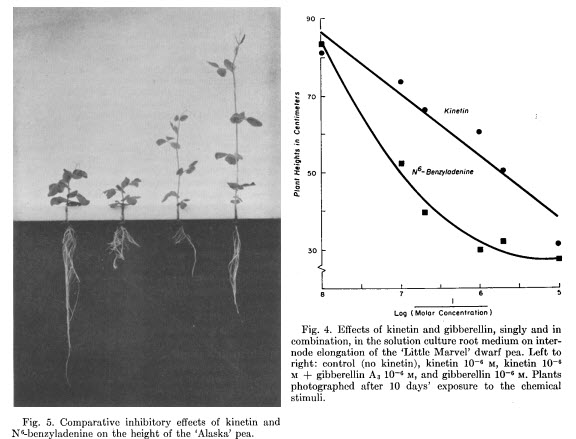
The effects of exogenous kinetin
In tissue culture, what kinetin does seems to be clear, it promotes cell division in the presence of auxins. However, for large plants in soilless media, the effect does not seem to be that straightforward. One of the first thorough studies of kinetin in flowering plants was done in the early 1960s (2). In this study, tomatoes, cucumbers, and peats were grown in solutions containing different concentrations of kinetin, going from 10-5 to 10-7 molar. The researchers showed that kinetin in solution behaved like a gibberellin inhibitor, directly suppressing plant height as a function of concentration. The plants developed several root abnormalities and changes in their flowering cycle, with kinetin inhibiting flowering in tomatoes, but accelerating it in peas.
You can see in this study that the effective concentration is quite low. The range of kinetin concentrations tested goes from 0.0215mg/L to 2.15 mg/L. These values are quite small compared to the amounts of other hormones, such as IBA or NAA, generally used in plant culture. The concentration of kinetin plays a key role in its effect. A 2008 study on red goosefoot (3) shows the strong impact kinetin concentration can have. These researchers showed that low concentrations of kinetin increased bud formation and increased the height of the apical meristem, while large concentrations inhibited flowering and made the plants shorter.
The entire literature on exogenous kinetin applications is therefore split between apparently contradictory effects. Some studies show effects that are more in line with a gibberellin inhibitor, with shorter plants, while others show stimulation of shoot growth. What you get is dependent on concentration and plant species, making kinetin a hard hormone to use. Use too much and you might compromise flowering and yields, use too little and you might have undesirable elongation effects or simply no effects at all (4, 6).
Kinetin can also have an effect on the sex determination of plants. For example, kinetin induces female flowers in cannabis and can ameliorate the production of male flowers in female plants (12).
Kinetin foliar sprays
The mode of application makes a big difference as well. While most of the root studies I read using kinetin kept their application rates below 3mg/L, many foliar studies explore kinetin application rates that are significantly higher. In this study (9), for example, they perform kinetin applications at 100 ppm. From the foliar studies I read, I found this study (7) particularly interesting. In it, kinetin applications at 2.5, 5, and 10 mg/L were done using foliar spraying on tomato, cucumber, and pepper plants.
The researchers found that the cucumbers had an excellent response to the 2.5 mg/L treatment, with taller plants, larger leaf area, and bigger yields, while they showed negative responses to the 10ppm treatment, with lower yields. While tomatoes showed a similar response, peppers gave their best results with the 10 ppm kinetin sprays. This again highlights not only that plants will respond negatively to excessive doses of kinetin, but that this response is significantly species-dependent.
Environmental conditions
Furthermore, environmental conditions can play a significant role in the effects of kinetin. This study (8) found that kinetin could help rice plants give better yields under carbon dioxide enrichment. However, this worked only for some of the varieties of rice used. For the varieties for which it worked, kinetin applied as a foliar at 10.75 ppm was able to enhance the carbon dioxide fertilization effect.
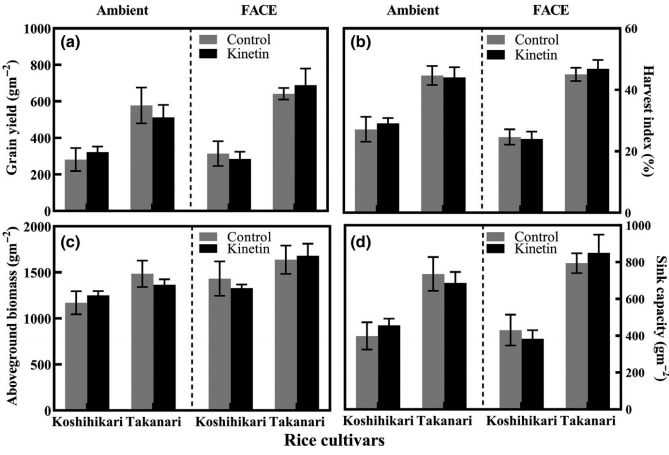
Other environmental conditions, such as salinity stress and oxidative stress, can also play a big role in the effect of kinetin. As a strong antioxidant, kinetin can help plants deal with oxidative stress (10). It has also been tested many times as a way to deal with salinity-induced stress, for example, see this article on kinetin applications in soybeans (11). In this last study, you can see how kinetin upregulates the gibberellin biosynthesis pathway when it was actively suppressed by the high salinity. Some effects, such as the production of jasmonic acid, are actually opposite in the control and in the salinity-induced environments as a function of kinetin concentration.
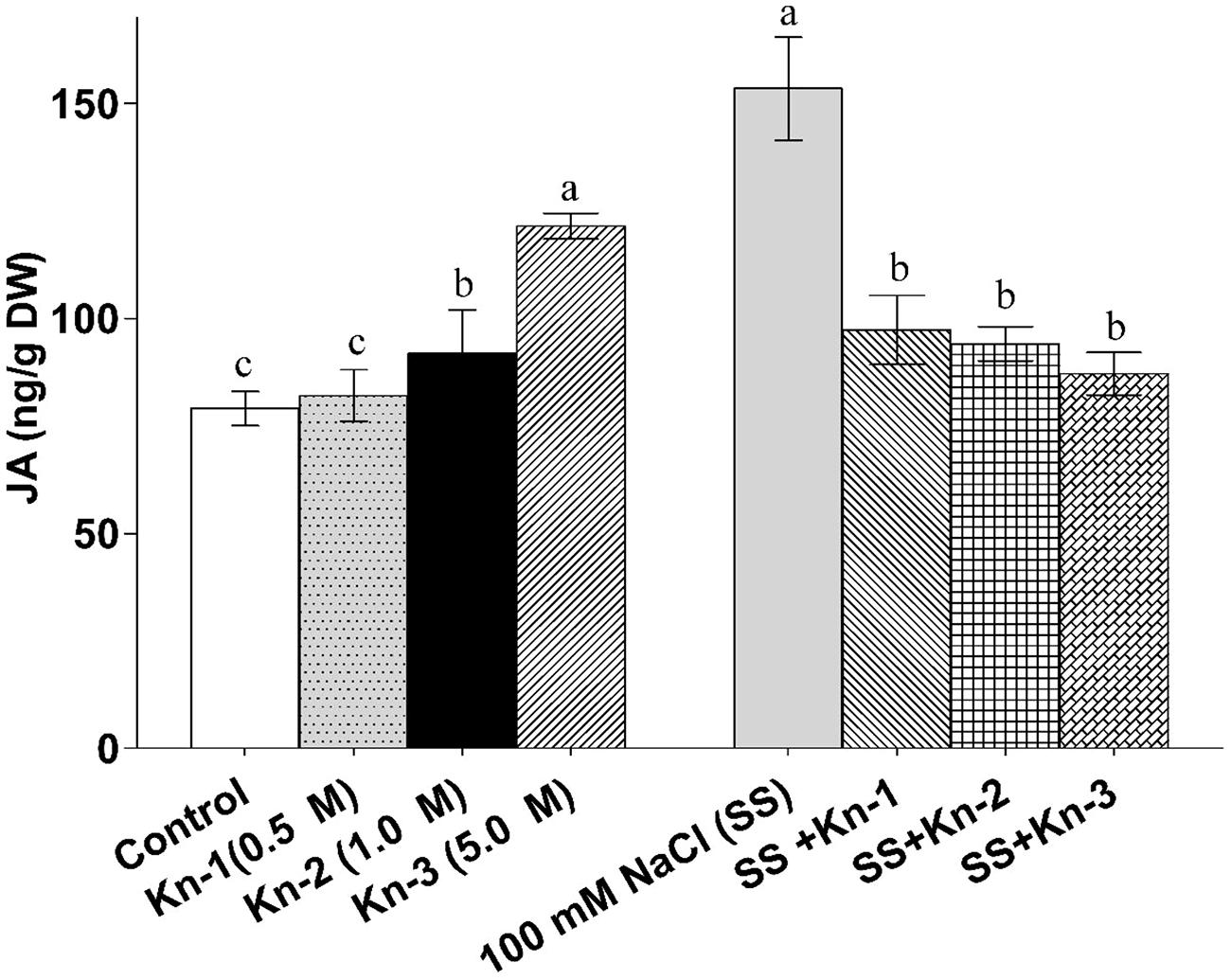
Conclusion
Kinetin can be a powerful and versatile hormone in flowering plants. It can be used to achieve a variety of different effects, including making plants shorter, increasing budding sites, increasing yields, or relieving sources of stress. However, the choice of concentration, method, and application time is critical and can lead to completely opposite effects if not done correctly. Low applications tend to increase growth and leaf area, while larger concentrations will show an effect similar to a gibberellin inhibitor. However, the concentrations that work best for a given plant cannot be known before experimentation is done. However, do consider that higher concentrations consistently lead to decreases in yields.
If you want to use kinetin in your crop, start with a foliar dose at around 2ppm and take note of the effects. From there, you will be able to gauge whether you want to have a higher or lower concentration of kinetin. If the dose is too high, you will start to see some negative effects. Also, time your applications so that they are in line with the effects you want to achieve. If you want to feed kinetin through the roots, use an even lower concentration and make sure your applications are properly timed, avoid having permanent exposure of roots to kinetin, as this is likely to be negative.
Have you ever used kinetin in your crops? What concentrations have you used and what effects have you seen? Let us know in the comments below!