A cost analysis of fertilizers for hydroponic/soilless growing in 2022
Why fertilizer costs matter
Fertilizer can be one of the largest expenses of a hydroponic growing facility. This is especially true when boutique fertilizers are used, instead of large scale commodity fertilizers. The use of non-recirculating systems with high nutrient concentrations also contributes heavily to high cost fertilizer usage. A medium scale growing facility working with boutique fertilizers can in some cases spend 2000-4000 USD per day. Even when using some of the most cost effective solutions, a facility can still spend 4000 USD per day if they use 20,000 gal/day with a nutrient line costing 0.2 USD/gal.
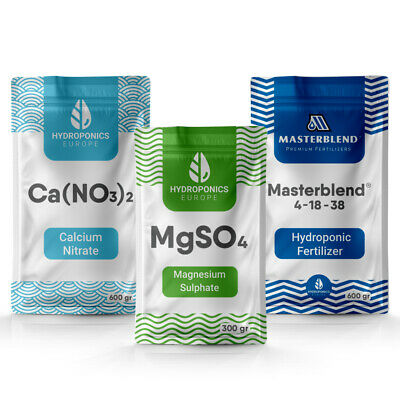
In 2022, the high cost of energy and high inflation have increased raw fertilizer input costs to the highest point of the past decade, making the problem of fertilizer costs even more pressing. This has been specially the case for soluble phosphate fertilizers which have, in some cases, seen costs triple from the start of 2019. This is because soluble phosphates were largely produced in Russia and alternative sources of soluble phosphates had a hard time ramping up capacity at the same cost level as could be previously achieved.
To help people who are growing better assess their costs, I seek to paint a clear picture of the current cost level of commodity and boutique fertilizers as well as the cost levels that can be achieved with preparation of custom solutions.
Price sources
The cost analysis focuses on the US market. The prices I obtained for boutique fertilizers are from google searches where I found the cheapest costs at the highest scale I could find. For commodity fertilizers I used the price points of customhydronutrients.com, which is a trust-worthy website for the purchase of fertilizer inputs. These prices are also accessible from small to large scales, so they do not require large scales to be accessible. Boutique fertilizer companies might offer larger discounts to people who contact them directly to buy large amounts, but I did not use these prices as they are not publicly available.
To make comparisons easier, I will express all costs as costs per final gallon of nutrient solution, when prepared per the directions of the manufacturer or to arrive at formulations with a reasonable composition (formulations that can grow healthy, high yield crops). Please also note that I only considered fertilizers that could be used to prepare concentrated solutions to be used for injection, as these are fundamental to large scale growing operations. I also only considered powdered fertilizers as these offer the lowest cost. Liquid concentrated fertilizers – which are often substantially more expensive – were not considered.
For purposes of keeping the costs as low as possible I also only considered the base products from boutique fertilizer companies and did not consider the costs of any of their additives (line cleaners, boosters, hormones, etc). Shipping costs are also not considered here.
Blended fertilizers
The easiest, most accessible fertilizers for most people will be pre-blended fertilizers. Due to the proliferation of the cannabis industry, most of the pre-blended fertilizers that are sold to retail growers will be cannabis-centric and will have a considerably higher price than the blends currently used by the wider hydroponic industry.
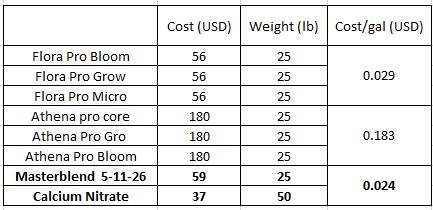
The table above shows three representative fertilizer programs for comparison. The Flora Pro series from General Hydroponics was the lowest cost boutique fertilizer I could find, with a total cost of 0.029 USD per gallon at the recommended dosing rates by General Hydroponics. I also put the Athena line for comparison, as they often portray themselves as a low cost option for cannabis companies. Their cost is almost an order of magnitude higher, at 0.183 USD/gal. From this analysis it seems clear that their margins are much higher than those of General Hydroponics although they can be substantially more cost effective than other companies with even more expensive products.
After seeing the above table, it is clear that boutique companies are not price competitive against formulations using traditional blended fertilizers from the agricultural industry. A formulation using Masterblend 5-11-26 and Calcium nitrate, which could be perfectly adequate for the growth of flowering plants during their vegetative stage or purely vegetative plants like basil, has a cost of 0.024 USD/gal. Similar simple approaches using other blended products can be used to achieve a variety of compositions at a similar price tag.
Raw input fertilizers
It is also interesting to consider the case of raw fertilizer inputs as this allows us to better think about formulations to reduce cost and also calculate whether making custom fertilizers is worth the expense. The table below shows you some commonly used bulk fertilizer inputs, their cost in USD and the cost per pound of each one of the products.
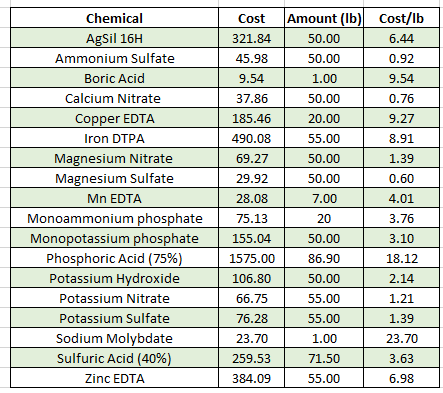
Micronutrients are the most expensive per pound, but since they are used at very low amounts, their total cost contribution to fertilizer solutions is often less than 0.002 USD/gal (not counting the iron). The cost of the bulk fertilizers is much more important from a cost impact perspective. From these fertilizers, potassium inputs are often the most expensive. Both potassium nitrate, potassium sulfate and monopotassium phosphate are usually large contributors to the total price of a hydroponic formulation. Soluble silicon amendments, like AgSil16H, are also often large contributors to the overall price of these formulations. The above analysis also shows that Phosphoric acid is a very expensive option for pH adjustments in hydroponics. For this reason – and a few other reasons out of the scope of this post – sulfuric acid should almost always be used.
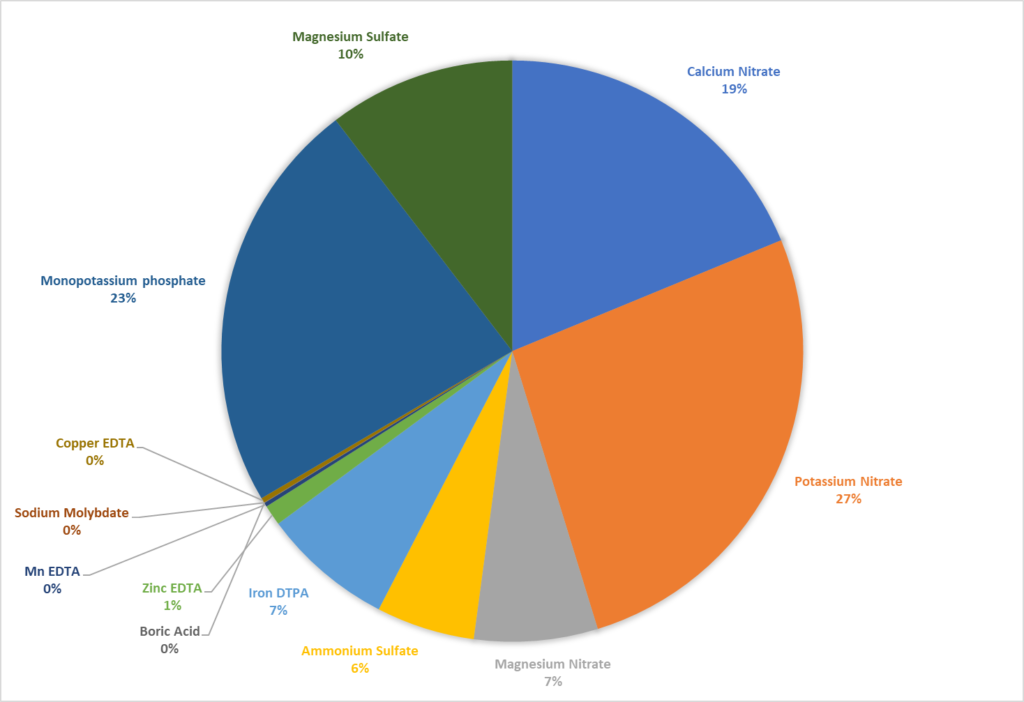
The image above shows you the bulk contributions of all the raw inputs used in a sample custom formulation. The total cost of this formulation is around 0.016 USD/gal. If we supplemented Silicon from AgSil16H, the cost of this formulation would likely increase to close to 0.025-0.03g/gal depending on how much Si we would like to add. You can see here that the highest bulk costs are indeed the monopotassium phosphate and the potassium nitrate, it is unlikely that we would be able to diminish this cost contribution substantially, as this is the true bottom line of the fertilizer industry.
For most of my clients, formulation costs in real life will usually be between 0.01-0.03 USD/gal. The final cost will depend on which bulk discounts are available at scale, which plants the client is growing, what the cost of shipping the fertilizer is and which additional amendments beyond simple raw fertilization we choose to use. Sometimes, by using the nutrients already present in the water, substantial additional savings are possible with custom formulations.
Note that the above raw input analysis does not include the cost of labor to prepare the concentrated nutrients needed for injection. If a worker needs to spend a couple of hours per week mixing 25 gallons of each fertilizer then this, at 20 USD/hour, would likely increase the cost of the fertilizer by around 2-5%. Since workers can often mix batches of concentrated solutions that end up creating thousands of gallons of solution, the labor cost needed to mix fertilizers is often not meaningful relative to the overall cost of the inputs.
Balance between complexity and cost
From the above, it is clear that making your own fertilizer has the lowest cost, even at a small scale. However, it does add a substantial level of complexity to an operation and exposes the operation to a variety of potential mistakes dealing with preparation. A careful consideration of the advantages and disadvantages of mixing your fertilizer needs to be made. For large facilities, I believe this to be a no-brainer. At scale, it almost certainly makes sense to mix your own fertilizers.
However, it is true that at a medium scale, a grower might benefit from not doing their own mixing, as this simplifies their operation and allows them to focus on growing great plants while they grow. In this case, you can certainly – regardless of the plant you’re growing – create a formulation based on a widely available agricultural industry blend with perhaps one or two raw inputs, to achieve a highly cost effective formulation.
Of course, there is also an additional cost to fertilizer formulation, which – per the prices charged by myself and other colleagues – might cost you from hundreds to thousands of dollars depending on complexity. If you do not want to incur this cost, then you should bear in mind you will pay a perpetually higher price in your fertilizers, to a company that has done the formulation work for you.
At a large scale, you definitely do not want to go with a formulation that reduces the yield or quality of your plant product, so – if you lack the experience to do these formulations yourself – always make sure to hire someone who knows what they are doing.
In the simplest case, a formulation schedule of an agricultural preblended product – using for example the Masterblend 5-11-26 mentioned above – adjusted to your situation might lower your costs by an order of magnitude from an expensive boutique shop at a minimal increase in complexity and low formulation costs. Of course you can always make your own Masterblend proxy as a first step when you move to fully custom formulations. If it is not possible to use these types of blends – due to for example your water composition – a fully custom formulation will be required.
There is no reason to pay even higher prices
People in the traditional large scale hydroponic industry have been growing at very cost effective fertilizer prices for decades. If you are a small, medium or even large scale grower, there is no reason why your fertilizer costs should be astronomically high. There are no reasons to perpetually pay high margins to fertilizer companies and there is no reason why you shouldn’t take advantage of the easiest cost savings that can be achieved with products that are already available to the bulk agricultural industry. Now that the raw fertilizer input costs are even higher, it is more important than ever to go to lower cost methods to achieve your desired hydroponic formulations.
If you want to learn how to make your own fertilizers, then I advice you visit my youtube channel or read my blog articles on making your own fertilizers from raw inputs.
Are you using boutique fertilizers? Are you mixing your own? Please let us know about your experience in the comments below!